There are two basic strategies for building a cork grip for a fly rod. The first involves gluing the rings directly onto the rod blank and then shaping the grip. Another way involves gluing the cork rings together off the blank, and then shaping the grip in a lathe setup before reaming and fitting to the rod blank. That process is described by Bob Petti in this article.
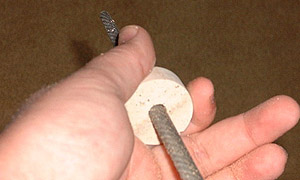
A rattail file is used to ream out each ring to the required size. Files of different sizes can be used for various blank diameters.
All the rings have been bored to fit the blank. Notice that some rings have more defects than others, although these are all from the same "quality grade" shipment.
For uplocking grips with an inlet hood, I glue the first two rings together first, to avoid crushing the thin walled ring that accepts the reel seat hood.
Not a lot of pressure is required to glue those two rings together. The weight from a jar of water is sufficient. Leave these to dry overnight.
Now we have all we need, the individual bored rings and the inlet ring assembly.
The faces of each opposing ring are painted with glue and compressed on a threaded rod fitted with a washer and nut on each end. Apply enough pressure such that the glue begins to ooze out between each ring.
Glued rings on threaded rod, chucked into our lathe setup.
The first chore is to turn the rings down to an even cylinder. A flat board and rough sandpaper make this a quick job.
Starting with 60 grit sandpaper removes the cork quickly but leaves a rough surface. Note the portions of some rings that have not been touched by the sandpaper, telling us we still have more sanding to do to get a uniform cylinder.
Periodically check the diameter of your cylinder until we have reduced the size to just slightly larger than the desired diameter of the finished grip.
The grip is shaped and polished with progressively finer grits of sandpaper. My final polish is done with 320 grit.
The finished grip, fresh off the lathe. Note that while the cork was not perfect (pit free), it's not too bad. This is certainly a fishable grip. Note also the lack of glue lines.
All these grips were done on the same lathe setup. The beauty of turning your own grips is the ability to size and shape them to fit the angler and the rod being built.
There are two basic strategies for building a cork grip for a fly rod. The first involves gluing the rings directly onto the rod blank and then shaping the grip while the blank turns in some sort of lathe setup. My friend Dave Lewis provided an excellent tutorial on building grips in this fashion. Another way of making a grip involves gluing the cork rings together off the blank on some sort of mandrel, and then shaping the grip in a lathe setup before reaming and fitting the grip to the rod blank. That is the process I will describe here.
Selecting Cork
The first process in building a rod grip is selecting the cork. As with any other natural material, cork quality is not consistent from ring to ring within a batch, and it is also available in a number of quality grades. For the most part, the variations and "quality grade" of the rings refers to the number of defects in the cork. Holes in the cork will result in pits in the finished grip that may need to be filled depending on the severity of the flaw and the needs of the builder. Very high quality cork has minimal pits, none of which will be so severe as to require filling after the grip is shaped. At the other end of the spectrum, lower quality cork is filled with holes, many of them large. A fine grip can still be made, but the builder should take care to fill the pits in the finished grip with a good filler mix.
Good cork is getting hard to come by and has seen a corresponding increase in price - as much as nearly two dollars for a single ring which could result in a finished grip price of almost thirty dollars. Cheaper cork is readily available and ranges in price from less than half a dollar per ring to a dollar per ring. Regardless of quality, buying your cork rings in bulk, usually in lots of 100, will offer some savings and allow the builder to hand select the individual rings for a particular grip.
Let's assume for this article that we're using good cork with some defects but nothing that will cause us to worry about filling pits. We'll leave that for another day.
Prepping the Rings
After you have decided on the length of the grip, which will dictate the number of rings used, the next factor to consider is the inside bore of the rings. Since the rings will be assembled on a mandrel (in our case a threaded rod) which are available in a variety of diameters, I like to match the mandrel to the rod blank and then ream out each ring to fit the mandrel. This makes the final fit of the grip to the rod blank a fast and accurate process. I measure the outside diameter of the blank where the topmost ring will eventually be installed, and then choose the threaded rod that most closely approaches but does not exceed that size. For example, if the diameter of the blank 10.5 inches up from the butt end is 22/64, then a 5/16 threaded rod would be my choice.
I hand ream each ring to fit the mandrel. Lucky for us, round tapered rattail files are sized to match the threaded rods we'll use, those being 3/16, 1/4, 5/16, and 3/8. Some rings have bore sizes of 1/8, but the most common is 1/4, so if you find your rod blank to be between 16/64 and 20/64, you can use the cork rings unmodified. Each ring is then bored to size and slipped onto the threaded rod.
Glue Up
Once the rings have been bored to size, they need to be glued up and clamped tightly together. Certainly, you can use any of the popular epoxy products to accomplish this. Household epoxies like Devcon will work, as well the epoxies made especially for rodbuilding. A favorite for this purpose is U-40 Rod Bond because it can be applied so sparingly to the cork surfaces, thus eliminating the chance of visible glue lines between the rings when the grip is shaped.
While epoxy will form the strongest bond between the rings, it will also form a strong bond with the mandel being used. In the case of a threaded rod like we're using, that means we'll have to go to heroic measures to remove the glued rings when we're ready to install the grip on the rod. I use high quality wood glue - Titebond II. It has several positive qualities. It is cheap, it is strong, it does not require mixing, and it stores well. It is also very waster resistant, which is of obvious important on a fising rod. One bottle will easily last a hobby builder a lifetime of building grips. The finished grips made with rings glued with wood glue do not show a glue line and are quite attractive.
Each ring is slid into place on the threaded rod and the washers and nuts are installed, but the rings are not yet compressed. At this point we need to apply glue to the opposing faces of each ring. Note here that I typically put a low grade ring on each end of the grip during the glue up and compression stage, because the washers will leave an indentation in the end rings when the entire grip is compressed.
Moving from ring to ring, I apply an even coat of glue on each ring face and slide one onto the other, until every ring has been glued up. At this point, I use a pair of wrenches and begin tightening the opposing nuts until the rings are compressed together. We want this to be tight, but not so tight that the end rings are damaged. Once we can see the glue oozing out between the rings, that's typically tight enough.
The only exception to this process is when I have a grip with an inlet ring in one end that will accept the hood of an uplocking reel seat. In this case, I assemble the first two rings off the grip to avoid crushing the thin walls of the ring that has been bored to fit the reel seat hood. When it comes time to assemble the entire grip, I use only a nut on that end, so the pressure is against the thick ring, not the one that has been recessed. Any deformation to that inner cork wall from the tightening nut will not be visible on the finished rod.
Any excess glue that has squeezed out between the rings is wiped off with a damp cloth and the entire assembly is set aside to dry overnight. The next day, I remove the nut and washer from one end and slide the grip off the rod. You'll notice that the glue has not yet dried on the inside of the grip, so I set this aside for another day or so to ensure the glue has dried thoroughly throughout the grip.
Shaping the Grip
One we have a bunch of rings glued up, we're ready to shape these into a grip. Instead of using the goopy glue-slimed threaded rod that was used to glue the rings together, I use a fresh one (they're cheap enough). I also keep one unglued threaded rod for turning, so I don't have to worry about trying to turn nuts on a threaded rod that has been all gunked up with glue.
Your lathe can be as sophisticated or as simple as you like. Lord knows I would love to have a good woodworking or metal lathe in which I could mount my grip for shaping, but my budget has forced me to make due with a cheap hand-me-down drill and a couple leftover boards. For turning cork grips, it does the trick, but it's not ideal. If I did more than a handful of grips a year, I'd want something else.
My dust collection system is of similar thrift. I turn my grips outside. I take the whole assembly out to my driveway and let the breeze blow the cork dust into the woods. I once turned a grip in the garage and watched in horror as cork dust settled on two cars and all the junk we store out there. Not too mention how much gunked up my sinuses and lungs. I tried a dust mask, but that just made my eyeglasses fog up. Either buy a good shop vac and fashion a dust removal system near your lathe, or do the work outdoors.
The first chore in shaping a grip is reducing the cork to a uniform cylinder of a specific outside diameter. For this, I use a flat board which has a sheet of 60 grit sandpaper stapled to its face. Checking the outside diameter of the cylinder periodically, it's a quick matter of removing enough cork to begin the shaping process. The shape of the grip is roughed out with strips of 60 or 100 grip sandpaper. What we're
aiming for is the final shape, but sized a little larger than what we want the final grip to be, as some cork will be removed by final polishing.
Once you've obtained the shape you want, the process can go in one of two directions - final polishing or pit filling. As we stated earlier, we're going to assume we're working with cork that does not have such severe pits that we need to use a cork filler. If that's not the case, now is the time to remove the grip from the lathe, clean the cork dust from the shaped grip, and fill the pits with your filler so they can be sanded smooth during the final polishing steps.
To finish off the grip, we need to polish it with progressively finer grits of sandpaper until we have the baby bottom smooth finish we're looking for. How far you take this process is entirely up to you. I've found that going to 320 grit paper is far enough for my work, as the final grip is smooth and soft and very pleasant. Once the grip has been polished, it is ready to be reamed and mounted on the rod blank.
A job well done.
- Log in to post comments
A great help. Thanks
A great help. Thanks for your assistance. Good simple instructions using affordable methods.
I don't know maybe s
I don't know maybe someone has thought of this but a simple piece of 1-1/4" ID pvc pipe (pretty cheap at the hardware store) would keep you from having so much rough sanding to do if you wanted a larger o.d. grip. you could simply put the threaded rod and the rings into the pvc pipe and this would align the outside of the rings as well.
this is a great page
this is a great page just what i was looking for to learn the process w/o spending a lot of money but with very valuable info. as just to how it is done. will write back with my success or even if i can't get it right. super well written article. this whole site is new to me, and it is the best all around site i have been on and i have been on a lot searching for more info. Just on my third bamboo rod but loving it.
stephen